When we can't eliminate the mold scale by using a variety of measures, we must strengthen the maintenance and maintenance of the
mold .
The mold surface is relatively easy to remove at the beginning of mold formation, so the cavity and exhaust passage must be cleaned and maintained at regular intervals (for example, after each batch of molding). It is very difficult and time consuming to remove the mold after forming a thick layer of mold after a long period of time without mold maintenance and maintenance.
The sprays used for the maintenance and maintenance of injection molds mainly include: release agent, rust inhibitor, thimble oil, glue remover, mold cleaning agent, etc.
The chemical composition of the mold scale is very complex and must be removed and tried using new methods such as general solvents and various special solvents, oven sprays, and caffeine-containing lemonade. An alternative peculiar way is to use rubber to clean the model track.
When hot runner molding and heat sensitive materials are used, the melt residence time will be lengthened, thereby increasing the risk of decomposition of the material to form mold scale. Clean the screw of the injection molding machine.
Larger flow channels and gates are used for forming shear-sensitive materials. Multi-point gates reduce flow distance, low injection speed, and reduce the risk of mold formation.
Efficient mold venting reduces the potential for mold formation and provides proper mold venting during the mold design phase. The automatic removal of the exhaust system, or the venting method that can easily remove the mold deposit, is the best choice, and the improvement of the exhaust system often leads to a reduction in mold scale on the mold.
A special non-stick coating is applied to the surface of the cavity to prevent the formation of mold scale, and the test should be evaluated to evaluate the effect of the coating. The titanium nitride treatment on the inner surface of the mold avoids the formation of mold scale on the mold.
Door skin is one of main products of Luli Group Co., Ltd(Mainland).Our high quality Door Skin is adopting HDF as basic material, surface laminated Natural Veneer, melamine paper or pvc. during vacuum molding machine, the high temperature and pressure, with one or two forming technology to produce.
Advantages of Door Skin:
• Eco-environmental
• More beautiful
• More convenient
• No cracking, no deformation
Usage of Door Skin:
Luli Group Co., Ltd adopting"Prodcution line, Ecological development", has been selected and favored by more and more customers. It is mostly used as the main material of door of Kitchen, Washing Room, Baching room etc.
Kinds of Door Skin:
• One forming Door Skin
• Two forming Door Skin
• Natural Veneer Door Skin
• Melamine Door Skin
• PVC Door Skin
Details of Door Skin:
Size: 660/720/820/920/1020/1050x2150
Thickness: 2.8MM, 3MM, 4.2MM
Material: HDF
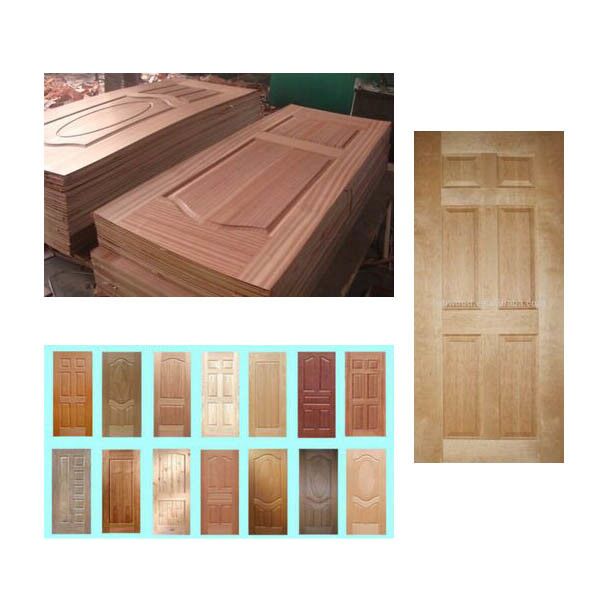
Door skin
Door Skin,Veneer Door Skin,Wood Door Skin,Door Panel Skins
Luli Group Co.,Ltd. , https://www.plywoods.nl