The transmission sub-tank cone ring support plate (hereinafter referred to as the cone ring support plate) is a sub-box workpiece of a multi-speed transmission of a heavy-duty truck. It has a small load during the working process of the transmission, but cooperates with other gears to realize the function of changing the gear position. When subjected to a certain amount of friction, the internal teeth of the cone ring support plate are required to have a certain wear resistance. Due to the speciality of the precision matching of the cone ring support plate with other workpieces, the precision requirement is high in the manufacturing process, so the deformation amount of the workpiece should be strictly controlled in the heat treatment strengthening section.
The cone ring support blank is forging and the material is 40Cr. The production process is: forging → preliminary heat treatment (tempering treatment) → machining → internal tooth strengthening → (finishing) → heat treatment. According to its service conditions in the actual working of the transmission, the technical requirements are that the internal tooth surface hardness reaches 50HRC or more, so that it has a certain wear resistance. Therefore, it is necessary to strengthen the internal teeth of the cone ring support plate. This paper focuses on the development and test of two heat treatment processes, ion nitriding and induction hardening, and compares their economic costs to select the optimal strengthening process.
I. Ion nitriding
Ion nitriding belongs to the surface modification technology of modern materials, also known as plasma chemical heat treatment or ion bombardment heat treatment technology. Compared with general gas nitriding, it has many outstanding features: high quality of the layer and controllable layer structure, strong controllability of the process, small deformation of the workpiece and short production cycle. After the workpiece is treated by ion nitriding, the hardness of the surface of the material can be significantly improved, so that it has high wear resistance and fatigue strength.
1. Ion nitriding process development
The cone ring support plate (see Fig. 1) has a thin wall thickness (thickness of 10 mm), and the inner teeth are parts that need to be strengthened. The wear resistance can be improved by ion nitriding. The process of ion nitriding is: workpiece cleaning → furnace loading → vacuuming → arcing → heating → heat preservation → tapping → detection.
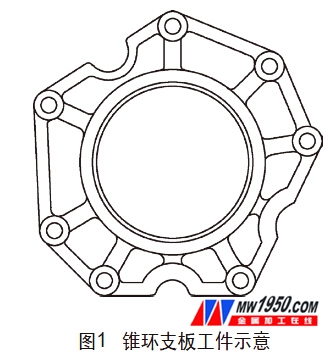
In the process of ion nitriding, the current and voltage parameters should be controlled during the temperature rising phase, and the temperature should be slowly increased. The heating, heat preservation and reheating steps can be repeated until (500±20) °C to reduce the deformation of the cone ring support during heating. The holding time is less than 4h, so as not to cause the nitride structure to be coarse, resulting in a decrease in surface hardness. The furnace loading capacity and the furnace charging method are properly installed according to the capacity of the ion nitriding furnace, the power of the power source, and the size and shape of the workpiece. The cone ring support plate is thin and parallel on both sides, so it is possible to use multiple layers of superimposed placement during furnace installation. Ensure the alignment when loading the furnace, use the pin or screw to block all the holes on the workpiece to prevent the glow discharge from concentrating during heating, the local current density is too large, and the temperature is too high, resulting in uneven temperature of various parts of the workpiece, thus affecting The quality of nitriding. The ion nitriding furnace and the control part are shown in Figure 2.
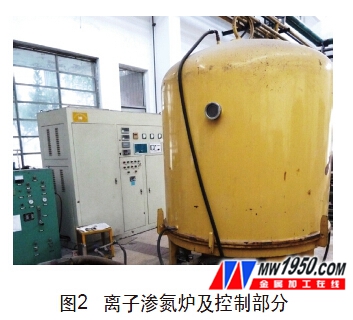
2. Ion nitriding results
After the ion nitriding process is completed, the internal tooth portion of the workpiece is sampled and inspected, and its surface hardness is 550 to 600 HV. The ion nitriding layer is composed of a compound white bright layer and a diffusion layer, wherein the white bright layer is 2 to 5 μm, and the diffusion layer is 0.15 to 0.25 mm; the relationship between the hardness distribution of the sample cross section and the depth of the nitrided layer is as shown in FIG. 3 . The final deformation of the inner teeth of the cone ring support plate is checked by a special inspection tool, and the roundness deformation amount is 0.05 to 0.07 mm, which satisfies the requirement of less than 0.08 mm specified in the pattern.
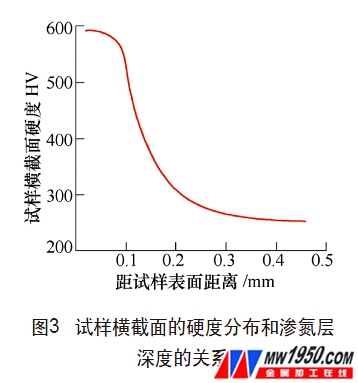
At the same time, the white bright layer compound after nitriding has high stability and high wear resistance, and meets the technical requirements of the workpiece. Therefore, ion nitriding can be used as a kind of internal tooth strengthening process of the cone ring support.
Second, induction heat treatment
Induction heat treatment is a commonly used local heat treatment process. It has a special heating method to obtain special effects that are difficult to achieve by conventional heat treatment. Therefore, it has the following advantages: fast heating speed, short time, high production efficiency; little scale and small deformation. The heat treatment quality is high, and the workpiece can be locally strengthened; the heating efficiency is more than double that of the conventional heat treatment, and the energy saving effect is good; the automatic production can be realized; the pollution-free, the production conditions and the production environment are good.
1. Development of induction heat treatment process for cone ring support
(1) Design and fabrication of internal tooth sensor of cone ring support For the speciality and technical requirements of the workpiece, the internal tooth is quenched and strengthened by induction heat treatment. The induction heat treatment of the cone ring support plate is carried out on a universal vertical quenching machine. The induction hardening method is a single heating quenching. A special internal tooth quenching sensor is designed for this purpose, as shown in Fig. 4. The sensor is mainly composed of a drainage plate, an effective circle (and a water sprayer) and other auxiliary parts. Since the current of the ring inductor is concentrated on the inner side of the effective ring of the inductor, in order to improve the internal quenching electric efficiency, a "Î "-shaped magnet is mounted on the inner side of the effective ring according to the notch effect of the magnetizer, and the current on the effective ring is applied. Pushing to the outside of the ring effective ring gives a good heating effect. At the same time, due to the short heating time, the effective ring does not pass water during heating, and the cooling of the effective ring is completed in the subsequent quenching and water spraying process.
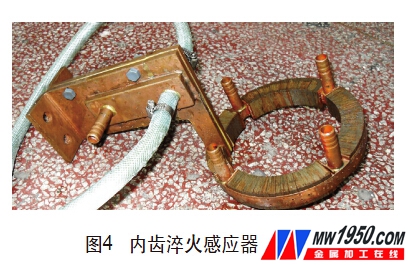
(2) Cone ring support plate induction heat treatment fixture design According to the shape and size of the cone ring support plate and structural characteristics, the quenching special fixture is designed to support and fix the workpiece during the quenching process. The middle bolt is changed to the positioning pin) fixed on the fixture. This method is similar to the quenching treatment in the ordinary heat treatment, which can significantly reduce the quenching deformation of the workpiece. The quenching tooling is shown in Figure 5.

(3) Inductive heat treatment process parameters of the cone ring support The cone ring support plate is heated to the austenitizing temperature and then spray quenched. The final induction heat treatment process parameters after commissioning and optimization are: current 155A, voltage 250V, load capacitance 1000kvar, transformer turns ratio 4:1, operating frequency 23kHz, heating time 9s, cooling time 8s, using 0.3% polyvinyl alcohol (PVA) Water-soluble quenching cooling medium, spray pressure is 0.15MPa. In order to prevent cracking and stabilize the size, after quenching, low temperature de-stressing and tempering is carried out for 2 hours, and the temperature is 180 °C.
Dimensional measurement of the cone ring support after quenching and tempering results in poor internal tooth deformation. Possible causes are low concentration of quenching cooling medium, large spray pressure, or unreasonable component structure. Therefore, the following measures are taken to solve: the concentration of water-soluble quenching cooling medium of polyvinyl alcohol (PVA) is increased from 0.3% to 0.5%; the spraying pressure is reduced from 0.15MPa to 0.10MPa; according to the shape and structure of the cone ring support plate, Optimize the design of the workpiece without affecting its use and assembly performance, making its groove structure as symmetrical as possible (see Figure 6).
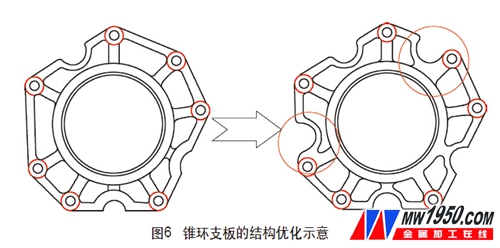
After the above three measures were taken, the induction quenching process test was carried out to verify that the deformation amount was controlled and the design requirements were met. Especially after the optimized design of the cone ring support plate, its use and assembly functions remain unchanged, the self-weight is reduced, the raw materials are saved, and the economic benefits are obtained.
2. Cone ring support plate induction heat treatment results
Non-destructive testing of magnetic particles in the inner teeth of the tapered ring support plate subjected to induction heat treatment, and internal teeth without quenching defects such as cracks. The hardness, hardened layer depth and hardened layer structure were measured for internal tooth cutting. The hardness of the hardened layer is 52-55HRC, the depth of the hardened layer at the bottom of the tooth is about 2mm, and the top of the tooth is completely hardened, as shown in Figure 7. The hardened layer structure is fine needle-like tempered martensite, as shown in FIG. At the same time, the deformation of the inner ring gear of the cone ring support plate is less than 0.07 mm, which meets the technical requirements.
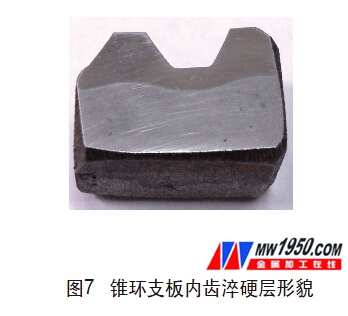
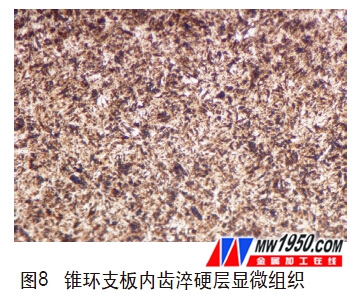
Third, the economic comparison of ion nitriding and induction heat treatment process
Both ion nitriding and induction heat treatment are energy-saving and environment-friendly heat treatment methods. After surface strengthening, the surface hardness of the material can be improved to a certain extent, so that it has high wear resistance, fatigue strength, etc., but at the same time satisfying the service conditions, Consideration should be given to strengthening process economic costs. It is estimated that the ion nitriding cost is 26 yuan / piece, and the induction heat treatment cost is 4.2 yuan / piece, according to the annual output of 30,000 pieces, the cost difference is 654,000 yuan. Induction heat treatment has an innate price advantage. Therefore, when the technical requirements and the deformation amount are simultaneously satisfied for the cone ring support plate, the relatively low cost induction heat treatment process is preferred.
About the author: Niu Enlai, Zhao Junping, Lu Fulai, Dongfeng Commercial Vehicle Co., Ltd., Technology Center.
Air purification Activated Carbon pore developed for chemical raw materials chemical synthesis gas, the pharmaceutical industry gas drinks with carbon dioxide and hydrogen, nitrogen, the inert gas such as hydrogen chloride purification and atomic facilities purification, also used to drop off the air pollutants and the classification of mixed gas purification.
Activated Carbon For Air Purification
Activated Carbon For Air Purification,Pellet Activated Carbon For Air Purification,Coconut Shell Activated Carbon,Decolorizing Activated Carbon
NINGXIA SINOTOPSKY INTERNATIONAL TRADING CO.,LTD. , https://www.nxsinotopsky.com