The vector control that appeared in the 1970s made the control performance of asynchronous motors greatly improved. In indirect magnetic field oriented vector control, accurately estimating (or observing) the magnitude and angle of the rotor flux is the key to the problem. Traditional flux estimators include voltage and current types. The voltage-type flux linkage estimator depends on the stator resistance, and the current-type flux linkage estimator depends on the rotor resistance. During the operation of the motor, the rotor resistance will change with the temperature rise (and the skin effect of the wire, etc.), which has a great influence on the estimation accuracy. In recent years, many scholars have proposed a method to reduce the influence of the stator rotor resistance perturbation on flux estimation. For example, use two kinds of estimators together, or improve the pure integral part of the voltage type estimator, and so on. However, these improved flux linkage estimators still include stator and rotor resistance parameters.
This paper presents a rotor flux linkage estimator that does not contain rotor resistance parameters. In other words, the perturbation of rotor resistance has little effect on the accuracy of the flux linkage estimator. In this paper, starting from the basic equations of the asynchronous motor in the new coordinate system, the rotor flux estimator based on stator current vector orientation is derived. Through digital simulation, it is verified that the estimator can still maintain high accuracy when the stator resistance is greatly perturbed. Finally, its application in indirect field-oriented vector control is discussed. It is considered that this method can be used in high-performance control of induction motors.
2 Rotor Flux Estimator Based on Stator Current Vector Orientation In the stationary (c) coordinate system, the basic voltage equations and flux linkage equations for asynchronous motors written in vector form are the electrical resistance and inductance of the Chinese Journal of Electrical Engineering; iV and Vr are rotors. Voltage vector, current vector, and flux linkage vector; for stator and rotor mutual inductance; called motor speed.
The rotational speed of the stator current vector is denoted as 1. Select such a "1-2 coordinate system", whose 1 axis coincides with 4 and lags behind 2 axes p/2, and makes the rotational speed of the coordinate system equal to 妫. Hereinafter, the following marks 1 will be used to distinguish the projections of the respective vectors on the 1 axis and the 2 axes.
In this coordinate system, the basic voltage and flux linkage equations of a vector-type asynchronous motor are oriented on the stator current vector is (as shown) due to the 1 axis of the 1-2 coordinate system, so: U=|is|, 7s2=.According to this, basic equations (3) and (4) are expanded, and it can be seen that, in addition to equation 1 in equation (5), the remaining 7 equations in equations (5) and (6) None of the Rs is included. Only the seven equations are used in the following derivation. Therefore, the derived flux estimator must not be exhausted.
Using equations (5), (6), after a simple derivation, the equation (7) equals both sides by the LmW! , Then, with the equation (9) on both sides of the equal sign, so as to obtain the differential equation of the 2-axis division of the rotor flux linkage assuming ¥v20, then the equation (8) can be divided by the equation (10). Afterwards, obtaining the differential equation of the 1-axis component of the rotor flux linkage or writing ¥r2=0 is a singularity of the system, but only occurs in very rare cases (such as start-up). In both simulation and actual engineering, a small number can be used to replace the zero crossing of ¥r2 without introducing too much error.
With the simultaneous expressions (11) and (13), the differential equations of the rotor flux in the 1-2 coordinate system after the orientation of the stator current vector can be obtained, which can be succinctly expressed as the stator current in the 1-2 coordinate system. The vector-oriented rotor flux estimation rash is hereinafter referred to as the novel flux linkage estimator, and its functional block diagram is shown.
Different from the traditional voltage-type and current-type estimators, the parameter W1.W1 is introduced in the novel flux linkage estimator constructed by (15), which is the rotation speed of the stator current vector. In the steady state, it is equal to the angular frequency of the power supply. In the dynamic process, the expression of W1 is the use of Hall sensors to obtain a very accurate stator current value. A new type of flux estimator is available for the current flux estimator. The new flux linkage estimator can be seen from the current flux linkage estimator. Depending on the rotor resistance, there is a large transient and steady-state error in the estimated results when the rotor resistance of the motor is perturbed. The new flux linkage estimator does not include rotor resistance parameters, so the estimation results are barely affected and the estimation error is close to zero.
When the stator resistance of the motor is increased by 50% under open-loop operation at the power frequency, the estimation errors of the new flux estimator and the voltage-type flux linkage estimator are as shown.
Estimation Error of New Flux Estimator and Voltage Flux Estimator The angle estimation error of the novel flux linkage estimator and the voltage type flux linkage estimator can be seen from the sum, since the voltage type flux linkage estimator depends on the stator resistance. Therefore, when the stator resistance of the motor is perturbed, the estimation results show large transient and steady-state errors. The new flux estimator does not include stator resistance parameters, so the estimation results are barely affected and the estimation error is close to zero.
4 Application of Rotor Flux Estimator Based on Stator Current Vector Orientation in Vector Control From the above, the rotor flux estimator based on stator current vector orientation (new type of flux estimator) has superior performance in open loop operation. . The main purpose of verifying its open-loop performance is to use it in a closed-loop controlled asynchronous motor speed control system.
The mathematical model of asynchronous motor speed control system was established in Matlab/Simulink and digital simulation was performed. The motor parameters were as described above.
In simulation, this paper uses the traditional indirect field-oriented vector control for estimating the amplitude estimation errors of the new type of flux estimator and the current type flux linkage estimator. When the current signal is not loud, the differential signal is tracked. Therefore, it can be calculated by measuring the sub-current.
It is worth noting that in the derivation process, the parameter Rs is avoided by the stator current vector orientation, and Rr is eliminated by stripping the term containing Rr. In the new flux estimator finally obtained, the expression of Vr1 is slightly complicated. , but in exchange for eliminating rotor resistance parameters. The introduction of a new parameter 1 implies the effect of the rotor resistance on the estimator, so that the estimator does not have a fixed rotor resistance parameter, thereby greatly reducing the influence of the parameter perturbation on the estimation accuracy.
3 Digital Simulation and Results In Matlab/Simulink, the motor and flux estimator models were established. Among them, the motor parameter is: Rs is loaded with rated load. The initial conditions of the simulation are: t=0, the current and flux of the motor are all 0. The motor runs in open loop at the power frequency, and the new rotor flux and current flux linkage estimator are 100%. The estimated errors are as shown.
Estimation Error of New Type Flux Estimator and Current Flux Estimator The Chinese Society for Electrical Engineering, flux amplitude command is 1Wb, speed command is 100prad/s. Rotor resistance is perturbed at the same time, its perturbation amplitude is Mx=50%, MfIOO%. In the simulation, the same PI controller is used. In the feedback loop of the rotor flux linkage, a voltage-type flux linkage estimator, a current-type flux linkage estimator, and a novel flux linkage estimator are successively used.
The error between the estimated value and the true value of the three flux estimators is as shown.
Voltage-type Flux Estimator New Flux Estimator Current-Mode Flux Estimator Rotor Flux Amplitude Estimation Error This is not the main problem to be solved in this paper, so there is no in-depth discussion on this, but it is known through research that inductance parameter perturbation and When the speed measurement error is small, the new flux estimator can still maintain good performance. If you add an appropriate correction link, you can better suppress the impact of these interference.
The rotor flux estimator based on stator current vector orientation proposed in this paper does not include stator and rotor resistance parameters, and can maintain a very high accuracy except for a few singularities. Whether it is open-loop operation or closed-loop operation, the performance of the estimator is hardly affected when the resistance of the stator rotor changes greatly. Compared with the traditional flux estimator, the new flux estimator has obvious advantages in anti-disturbance. With the accurate estimation of the rotor flux linkage as the basis, the key issues of the vector control of the asynchronous motor are solved, and various control strategies can play a better role, thereby realizing the high-performance control and operation of the asynchronous motor speed control system.
Straight Seam Steel Pipe
The straight seam pipe refers to the steel pipe whose weld line is vertically parallel to the steel pipe.Also known as straight seam welded pipe or straight seam steel pipe.The straight seam pipe is made by winding and welding the long strip steel belt of certain specification by high frequency welding unit.
According to the material and use of welded pipe classification
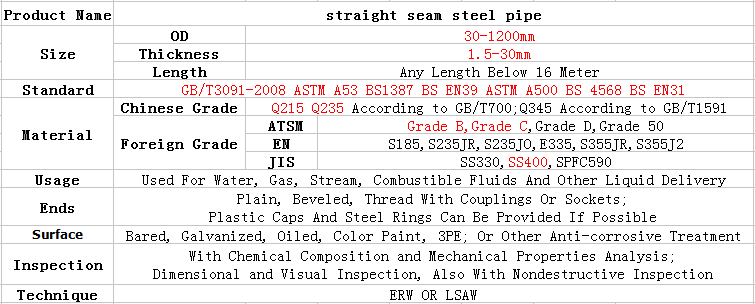
Packaging Details
Plastic caps on both ends, Steel bundle, Woven bag or acc. to customers' request.
Delivery Time
15 days after receiving deposit
If you have any questions, please contact with us directly and welcome you can visit our Factory.
Straight Seam Steel Pipe
Electric Resistance Welded Pipe,Welded Carbon Steel Pipe,Straight Seam Steel Pipe,Standard Straight Steel Pipe
HEBEI CHENGYUAN PIPE INDUSTRY GROUP CO.,LTD , https://www.hbcytube.com