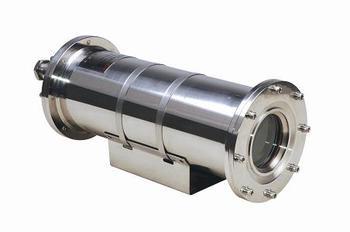
Let's take a closer look at the mine accidents that have occurred in China since the beginning of this year. On March 29 and April 1, 2013, two consecutive occurrences occurred in the Babao Coal Mine of Tonghua Mining (Group) Co., Ltd., Jiangyuan District, Jilin Province. Gas accidents caused a total of 35 deaths, 16 were injured and 11 were lost. At 2 pm on April 5, 2013, a flooding accident occurred at the Yunda Coal Mine Co., Ltd. of the Panan County Yunan Coal Coke Co., Ltd. in the Qiannan Buyi and Miao Autonomous Prefecture. It caused 6 deaths and direct economic loss of 10,302,800 yuan. At 14:15 on May 11, a gas explosion occurred at the Taozigou coal mine in Qi County, Zhangzhou City. Since 2010, China has successively experienced flooding accidents at the Shenhua Camel Hill Coal Mine, the flooding accident at the Wangjialing Coal Mine in Shanxi Province, and the gas explosion accident at the Yichuan Coal Mine in Henan Province and other major coal mine safety accidents....So many coal mine accidents have occurred. The livelihood of life is far away from us. Can we not do something to make people's production assets more secure? First of all, there are many problems in the monitoring system of coal mines. If relevant electrical and equipment systems are able to Doing well can also prevent similar things from happening at the source. Coal mine managers' indifference to life, negligence of safety personnel, illegal operations by operators, and violations of safety regulations by underground personnel will directly or indirectly cause coal mine safety accidents. However, most coal mine safety monitoring and control systems and equipment in China have problems. Can not be ignored. We do not dare to say that the informationization is much better and better, so that the occurrence of mine disasters can be avoided. After all, the reasons for the formation of mine disasters are too complicated, and special industries, management flaws, and small profits are the only small coal mines. However, if information is better, according to professional explosion-proof electrical equipment, explosion-proof cameras, etc., at least at the time of the accident, workers can run earlier, or rescue workers can find them faster.
At present, there are four major problems in coal mine movement monitoring system:
1. Most coal mine safety monitoring and monitoring equipment are backward and aging. China's large-scale installation of coal mine safety monitoring and monitoring systems was in the 1980s and 1990s, and the products are the first or second-generation coal mine monitoring equipment independently developed by China. Although some state-owned large and medium-sized coal mines have already upgraded these equipment and installed a new generation of digital monitoring systems, most coal mines are still using old-fashioned equipment and machines. Therefore, there will be hidden dangers in safe production. If not, Regular and timely inspection and maintenance of equipment can easily lead to safety accidents.
2. The information-based monitoring system and the new generation of digital monitoring systems are not well adapted to the downhole environment. The informatization and automation reform of many coal mine monitoring and control systems in China did not take into account the actual situation downhole. Although it achieved a large number of data acquisition, real-time transmission, processing and display functions, but its equipment itself also has strict requirements on the underground environment. . For example, the coal mine working face is the core of coal mining production, and it is also the occasion with the worst environment, the most frequent movement of people and equipment, and frequent accidents. However, the informatization transformation of coal mines adopts wired industrial Ethernet as the core, that is, the transmission of monitoring and monitoring signals on the working face is wired, but since the working face is a continuously moving working environment, the wired transmission method is difficult to adapt to this constant Moving and changing work sites have caused transmission cable damage and tearing from time to time due to various factors. In addition, the monitoring of the gob of working face in coal mines is less likely to be carried out by means of wired transmission.
3. The coal mine safety monitoring and control system is independent and does not form a synergy. The first batch of KJ series monitoring systems in China was developed by a number of research institutes. The new generation of digital monitoring systems developed by China in the late 1990s was also independently produced by different companies and institutions. There is no uniform standard for these products, and there is no uniform interface, which makes the system unable to be used in a unified manner. This has caused problems such as missing data in the monitoring project and inability to communicate properly between systems, which has led to the emergence of security risks.
4. The new sensor technology has not been fully applied to downhole testing. Taking the gas detection as an example, the existing coal mine methane monitoring devices mostly adopt the electrochemical method. This method has very high requirements for chemical components. The lifetime of general electrochemical components is only a few tens of hours, and they need to be replaced frequently to ensure the correctness of monitoring information. Once the gas inspectors are not replaced on a regular basis, they are prone to safety hazards. The problem of coal mine monitoring systems has existed for a long time. So what progress have been made in safety precautions? Small coal mines do not say for the time being. According to our understanding, most state-owned large and medium-sized coal mines do not have wireless digital sensors. Relevant persons said in an interview with this reporter that the state-owned large and medium-sized coal mines are "informative and can do as required." Well, we can only think that "requests" need to be improved. “No way, some standards were set more than ten years ago, and the latest one was around 2006. Last year, the state’s revision of the coal industry standards has already begun.†Zhao Duan said. PradeepK.Mohanty and MoiseNdoh first proposed to use WSN to realize the tracking and positioning of coal miners and underground environmental monitoring in coal mine shafts.
In China, China University of Mining and Technology was supported by the 2007 National Natural Science Foundation Project “Key Technology Research for Coal Mine Working Face Wireless Sensor Network Networking†and 2009 National Natural Fund Project “Long Distance WMSN Mine Multimedia Disaster Relief Communication Systemâ€. The wireless sensor network is used in underground coal mine monitoring and monitoring and underground disaster relief; the China University of Science and Technology under the auspices of the National Development and Reform Commission, establishes a study on the “CNGI and WSN-based mine underground positioning and emergency response linkage systemâ€, and conducts each miner through a wireless sensor network. Real-time positioning, expecting to achieve linkage with various disaster warning systems.
China University of Mining and Mining signed an agreement with the Xuzhou City Government of Jiangsu Province on March 15 to establish a “Sensing Mine†Engineering Research Center, which will gather scientific research forces of the entire university to research and develop the Internet of Things industry in order to apply the Internet of Things technology to coal mines as soon as possible. in. Let us look at the situation of foreign coal mines. We feel that there are zero mortality gas detection alarms in the UK. Our country also has, but it is expensive. It will not be equipped by everyone. It is usually carried by gas inspectors, and it is time to inspect. , there is a problem to notify the withdrawal by dispatching a telephone. Zhao Duan, a doctoral student at China University of Mining and Technology, said that the United States, the world’s second largest coal mining country, had 29 deaths in coal mine accidents in 2008, and the United Kingdom, Australia, and other countries even achieved zero mortality during coal mining.
In the United States, most of the dangerous excavation work does not require workers to climb downhole but instead uses machines to do the work. German mining workers carry a “gas detection alarm†when working underground, and once the gas concentration is too high, they will automatically report an alarm. Aside from the monitoring system, other coal mine equipment systems, in addition to gas detection alarms, there are many information devices that can be used are not used, such as digital sensors. We know that the underground working environment needs to monitor many environmental data, such as gas concentration, belt speed, turning speed, ventilation, and liquid level. Take the belt alone, it involves the speed, deviation, emergency stop device, temperature, CO concentration, etc., using analog sensors can only single transmission, while the use of digital sensors can transmit multiple signals at the same time, the transmission speed can not be the same day And language. Another example is wireless sensors. Wired sensors can be easily destroyed in a downhole complex environment. For example, a piece of coal may damage the sensor on the belt. Wireless sensors can largely avoid the problem of sensor failure and improve the accuracy of monitoring. Of course, some of the informationization we are looking for is still impossible. For example, each worker carries an electronic tag to achieve precise positioning. Although many manufacturers are so flickered, but in fact the current technology and products can only be a very rough position, equivalent to the punch in the general company, can only achieve management functions. Now that we use the Internet of Things to achieve accurate positioning, we must first tackle the problem of downhole wireless signal attenuation. Using wireless sensor networks and positioning algorithms to achieve accurate personnel positioning is also a research direction of some manufacturers and research institutions. Informatization, as an important means of supporting business and management, has achieved surprising levels in many industries in improving business response and management. We have reason to believe that information is not an illusion to help us protect the lives of miners.
Uhp 600 Graphite Electrode,Price Uhp Graphite Electrode,Uhp Graphite Electrode With Nipples,Graphite Electrode For Steel Plant
Carbographite Industrial PTE.LTD , http://www.carbographite.com