Abstract Thirty years ago, if you were the dispatch manager of a high-performance valve manufacturer in the United States, your daily schedule was very slow, and communication with partners was done by phone, fax or mail. Employees manually record inventory and check out shipments. Regular maintenance teams rely on human eye inspection,...
Thirty years ago, if you were the dispatch manager of a high-performance valve manufacturer in the United States, your daily schedule was very slow, and communication with partners was done by phone, fax or mail. Employees manually record inventory and check out shipments. Regular maintenance teams rely on eye inspections, drivers can communicate via two-way radio, if they are close enough, but in many cases, the only way to pass information about a particular shipment or a new receiving location is to have the driver check it on a regular basis. . These inefficiencies exist upstream and downstream of the supply chain, from the factory to the customer's facility. Very backward, prone to delays and high costs. The times have changed, and modern industry now relies on advanced machinery, advanced software and communication technologies, and modern management techniques that emphasize lean inventory and integrated supply chains.
What is the Industrial Internet of Things but there is another trend: buildings, factory equipment, vehicles, warehouses, pallets and workers themselves are increasingly connected to the network. Equipment ranges from tiny environmental sensors to complex industrial robots. The network they use may be wired or wireless. Some low-power devices will be battery powered or use Power over Ethernet (PoE) connections. Others must plug in or connect to the electrical system of the building. Many devices have their own firmware that can be updated or reprogrammed remotely.
In other words, sensors, controllers, and specialized devices now exist at the edge of the network, assigning unique IP or network addresses, collecting data, and performing a large number of notifications and tasks that extend enterprise capabilities. This is the Industrial Internet of Things (IIoT), which will transform the manufacturing, transportation, construction, mining and energy industries.
The IIoT practice is also based on high performance valve manufacturers. In the past, managers only asked for new inventory after getting off the warehouse, and needed someone to manually count. Orders for new parts are sent to the supplier via fax or courier, and a small number of people at each end handle paperwork and accounting.
Today, the same company can get more inventory checks, thanks to IIoT technology, such as a warehouse equipped with radio frequency identification (RFID) pallet tracking and the use of cameras and weight sensors to calculate the number of existing parts. These data are integrated with ERP and other software systems. When the supply of a component drops to a certain threshold, the system automatically submits the order to the supplier for replenishment. Employees rarely need to participate in placing orders, speeding up shipments throughout the supply chain and reducing labor requirements to replace the previous manual, high-touch process.
The efficiency of the IIoT can be extended to the transportation of finished valves. The days of truck drivers checking on the phone booth and paper list have passed. The company's IT systems now use optimization models to determine the most efficient use of fleets, track products across the country, feed real-time shipping data back to headquarters, and instantly deliver them to drivers via mobile applications or other devices connected to the network. . The RFID-enabled pallets are tracked as they leave the warehouse and loaded onto the truck and automatically registered at the customer's receiving center upon delivery.
Onboard sensors are part of an electronic logging equipment (ELD) system that monitors vehicle speed and driving time and even monitors the frequency of individual drivers using brakes, which helps save fuel, improves driver safety and reduces idle resources. If a truck driver performs a dangerous maneuver or drives for too long, the system alerts the driver and notifies the dispatcher. In addition, the ELD complies with federal monitoring requirements for drivers, replacing paper logs that drivers once had to fill out each day.
IIoT also enables better fleet maintenance. On-board sensors do not bring trucks to the repair shop for regular maintenance, but instead warn the fleet manager about specific vehicle problems. Trucks can be fixed or redistributed to routes that are easier to drive, reducing emergency repairs and shipping delays.
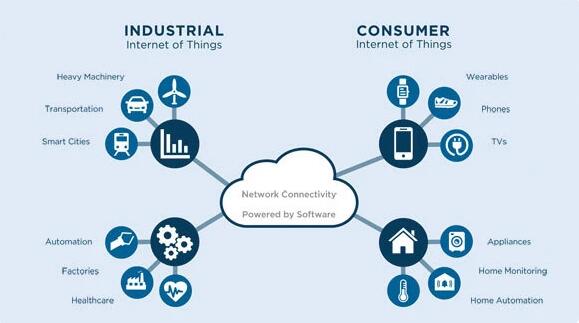
According to IDC, global spending on the Internet of Things (including consumer and industrial Internet of Things) reached $737 billion in 2016 and will grow at a rate of 15.6% per year to 2020. In 2016, the industries most invested in the Internet of Things included manufacturing ($178 billion), transportation ($78 billion) and utilities ($69 billion). Growth has entered the hockey stick effect (pre-sales are very low, there will be a sudden increase in sales at the end of the period): the number of connected devices has exceeded the population, Gartner expects to reach 21 billion connected devices by 2020, but Beecham Research Some sources pointed out that given the real world capacity constraints, including insufficient resource inputs, extremely high growth rates are impractical.
While some companies are wary of technology trends and vendor speculation about disruptive technology, IIoT is still a real trend that will affect many industries in the coming decades. Industrial suppliers have begun to prepare for the expected wave of IIoT and are looking at the huge opportunities in the vertical market. However, the challenge for companies is to choose to implement IIoT in their operations, and the resulting significant uncertainty.
Why choose IIoT
Although IIoT technology has existed for more than a decade, the concept of IIoT is different from IT before the IT and software revolution. If IT connects people, data and business systems, IIoT will evolve to provide IP connectivity to a wide range of sensor and machine networks, increasing productivity and bringing new insights to the business.
What is behind this trend? Of course, the latest technological innovations and application trends make IoT possible. PricewaterhouseCoopers believes that there are several factors that drive IIoT:
* Cheap new sensors * Faster processors * Cheaper storage * Can be integrated with open platforms * Suppliers and partners encourage adoption * Core business systems are more powerful * Data analysis and machine learning IIoT is more than just a technical story . Robert McCutcheon, head of US industrial products at PricewaterhouseCoopers, says many companies will not only reduce costs, but also speed up production and delivery, as well as a platform for growth and effective competition.
McCutcheon said: "IoT is mainly driven by the CEO and the board of directors," it has become a topic of subversion and competition in the conference room. Many discussions are centered around this topic. “What do our competitors do from a technical perspective? What do customers do from a technical perspective? What subversiveness we may have in this process, and what opportunities do we have to use and influence the market?â€
For IT managers, the wave of lIoT is subverting their traditional role. In companies implementing IIoT technology, IT cannot be limited to server room or desktop support. Instead, IT is increasingly seen as a key partner because equipment and sensors are active on the shop floor and in the field.
Indeed, the adoption of IIoT represents a redistribution of systems, processes and knowledge centers. IT managers and employees, as well as manufacturing, operations, distribution and supply chain management peers must get out of trouble, implement IIoT technology and get revenue. This is uncomfortable for some people, especially to give up power and share data outside of traditional isolated islands.
IIoT efficiency improvements and talent shortages Currently, industrial companies that are using IIoT are often designed to increase efficiency. The ability to streamline processes and connectable platforms is the primary goal of IIoT integration. At the Georgia Tech Manufacturing IoT Workshop, Andrew Dugenske, Director of the Center for Industrial Information Systems at the Institute, cited some areas that might be addressed by IIoT:
* Asset and inventory management * Capacity and performance monitoring * Quality analysis * Real-time alerts * Security and compliance * Throughput monitoring * Warehouse optimization Dugenske believes that corporate culture has a big impact on whether a team implements the Internet of Things. He said: "Companies that appreciate the benefits of the Internet of Things and are willing to invest in new technologies will achieve timely returns and competitive advantage." "Delayed companies will be in an insurmountable disadvantage."
Of course, as more and more companies move to IIoT, they will need more and more qualified personnel to design, implement and maintain the challenges of IIoT-based systems. McCutcheon said: "This requires new skills and is different from the traditional manufacturing environment."
Companies can work with external stakeholders such as local governments and vocational training centers to train technicians who can work in future factories. But McCutcheon warned that companies also need to overcome a perceived gap. McCutcheon said: "Historically, manufacturing is not necessarily the highest technology environment." "Manufacturers must change this concept. We now have some of the most technologically advanced jobs that are emerging, so it is also a way to attract talent. Not just training."

How to process all data? If the ultimate goal is to simplify operations, notify managers, and produce actionable insights, the data will need to be transferred, processed, aggregated, visualized, and stored. IT needs are very strong. Buildings or vehicles with a single IIoT may have thousands of sensors and devices that send data over a wireless or wired network connection. Data can be processed on the shop floor, remote campus or vehicle control system using chips or dedicated hardware. Data can also be converted or shared using APIs or custom software hooks, or placed in memory.
When such systems are extended to the entire company, including its core campus and satellite facilities, partner locations, remote sites, fleets and employee equipment, it is clear that IIoT has a large data dimension. This means that a large amount of data methods are needed to ensure data usage, such as moving to cloud-based applications and storage.
Companies that do not take full advantage of the data they have available will have real risks. According to McKinsey's report, only 1% of oil rig data will have 30,000 sensors. This is because sensors are primarily used to detect problems, not optimization and predictive analysis. This wastes big data.
There is also a safety perspective for IIoT. This is still an unknown area for companies dealing with network security in data centers, office systems and personal devices. In the IIoT environment, more attention needs to be paid to protecting devices, data, communications and processing capabilities far beyond the traditional IT landscape.
The nature of IIoT hardware, software and network connectivity has led to some unexpected security consequences. Many low-cost devices, such as remote cameras, routers, and even DVRs, have limited security features (including hard-coded default passwords and telnet access), or never update patches. Once compromised, they will cause problems such as DDoS attacks and malware distribution. An annoying IIoT botnet called "Mira" has been around the world and remains a problem today.
Integrated llot
As you would expect, the launch of the entire enterprise-wide IIoT system is very complex. Requirements include low cost, powerful sensors and other devices that can be integrated with existing systems. The administrator must also determine how the device is powered and connected to the data network. In fact, the system architecture may need to be modified to accommodate IIoT, and there may be significant integration challenges.
Dugenske of Georgia Tech said: "IoT requires sensors, bandwidth, processing power and communication capabilities to be reduced." "But it does not solve a critical problem: What are the specific data structures and protocols used? These huge cost-driven Factors are usually ignored.
In theory, whether you are dealing with a general-purpose controller or a specific industry product, the IIoT standard can alleviate integration. Companies can turn to products built on existing standards, whether they are global IT standards (such as 802.11ac) or products developed for industrial use, such as IEEE Standard 1377-2012 for electricity meters.
This has also promoted the formation of the alliance and promoted the development of new standards. They include the Industrial Internet Alliance, which promotes the common architecture, interoperability and open standards of energy, healthcare, manufacturing, transportation and smart cities.
It is unclear which standard will dominate, but this is a problem that has a major impact on IIoT. It is estimated that by 2020, LPWAN will reach 345 million times (about 26% of the total). Uncertainty leads to potential integration problems and encourages some industrial companies to “wait and see†before placing a bet on a product line or technical standard.
Llot's future industry is still in the early stages of the big wave of technology transformation driven by llot, big data and other emerging technologies. This is not a hype, but an inevitable consequence of the advancement of software, hardware, networks and systems in almost every sector of the global economy.
Some companies are already using IIoT to increase productivity and develop new products and services. As more and more advanced sensors, processing power and data storage prices continue to fall, mainstream industrial companies and their competitors will turn to IIoT to remain competitive and look for new growth opportunities.
However, there are still serious obstacles. Concerns about security, staffing and interoperability can put some industrial companies in trouble. Others may have questions about benefits, costs, and return on investment. Some technologies are still in the early stages of development, which is hampered by the uncertainty of standards or technical and physical constraints such as batteries.
Introducing new technologies into the workshop or assembly line, entering the vehicle maintenance and remote sites is also a challenge. Modern industrial equipment is complex and powerful, but most of them are not yet connected to IP networks. In addition, there are some types of industrial machinery that are often used in very vertical applications in the vertical field that few people know. These machines may not have llot capabilities in the next few years. Replacement or modification is possible, in fact, as the speed of the transition accelerates, this will be necessary. But for today's business or IT managers, that day may seem far away. In the 2015 manufacturer survey, nearly half said they did not plan to use smart sensor data to improve manufacturing and operations.
Some people show caution and others see a huge opportunity. Forward-looking industrial companies and startups in energy, transportation and manufacturing are investing heavily in IIoT and big data. These companies want to be prepared for the future, using IIoT to gain significant competitive advantage or develop new products and services.
Imagine a world of sensors, systems, data and even ubiquitous robots and artificial intelligence. Assembly lines, supply chains and remote sites will be run primarily by autonomous devices and algorithms, reducing delays and increasing worker safety. Self-driving cars on the road and in the air will be able to “talk†to the pallets they are transporting to better monitor their content and coordinate delivery. This is not science fiction, it is all possible through lloT.
Modern sweeping linear style. the towel racks are finished in high quality white finish. The only place to dry your towels neatly. It is not just about functionality and design, but also quality: this rail will last for years to come.
Towel Rack,Hand Towel Holder,Towel Bar,Towel Hanger
Kaiping city Pinsen Sanitary ware Co.,Ltd , https://www.corpthen.com